When the C2 Corvette generation hit the streets and racetracks in 1963, the all-new chassis took the world by storm. That chassis design carried over for 1964 production and was so advanced that it would continue through the C3 generation, serving for just shy of two decades. That said, the last time GM slid this chassis design under a Corvette was more than four decades ago, so it goes without saying, there have been improvements since then.


The car was a “driver” when Kevin purchased it. The original frame and drivetrain were removed to make room for the Street Shop chassis featuring the 650-horsepower LT4 engine.
There’s no denying the appeal of the 1964 Stingray Corvette’s styling. This white coupe may serve as the perfect example of how one might infuse today’s technology while keeping all those glorious lines intact. That is precisely what Kevin Wilkinson, the car’s owner, and Tim Ames of J&M Enterprizes, sought to do as they planned this car’s build. While the restomod concept isn’t new to Corvettes, the exacting level of detail given to this build is one of the key elements that set it apart. The Stingray generation’s classic lines speak for themselves with this build, as many of the car’s modifications would go unnoticed if they weren’t pointed out.
Closing The Corvette Generation Gap
Kevin’s car started as a “driver-class” Corvette owned by another J&M customer. He was looking to sell the car, and Kevin bought it as the base of this build. Even though the car could be driven, it was far from what Kevin and Tim envisioned. The planned modifications cut right to the core of the car, and it was quickly disassembled to its very foundation.

C2 Corvette bodies started with a floor, and other components were added as the body moved down the line. The modifications for Kevin’s car were so foundational that Tim needed to strip the body back down to step one to make the changes.
When the bodies were created for the C2 Corvette generation, the assemblers began the process of building the body from the floor up. For this rebuild, Tim would also need to start from the very beginning. Kevin was quite accustomed to the comfy seats in his C7 Corvette and wanted that same level of comfort in his C2. Kevin wanted to use C7 seats, but they are much taller than the factory units and hit the roof.


The C7 Corvette seats didn’t fit the car, so Tim lowered the floor to match the bottom of the frame. He also separated the firewall and seat mounting even further to give Kevin enough room to settle into the Stingray’s interior. The entire floor was removed to make these changes.
Neither Keith nor Tim wanted to cut them down, plus Kevin needed extra legroom. The answer was to drop the floor down even with the bottom of the chassis, move the floor pan and seat mounting area rearward an inch, and relocate the firewall forward to allow more legroom. With the cabin now made comfy for Kevin, the process of rebuilding the body with all new components and then filling them with modern bits could begin.


The floor was lowered to match the bottom of the frame rail to give Kevin as much headroom as possible. Tim then began rebuilding the body, including the entire “birdcage” metal frame.
As you can imagine, Kevin would not have been happy with decades-old performance while surrounded by the modern look and feel of a much newer Corvette. A complete Street Shop chassis full of C7 components and fitted with a supercharged LT4 engine and six-speed transmission was ordered to rectify that. The craftsmen at Street Shop raised the C7 suspension’s mounting points on the new frame to allow for a lower ride height once the body was installed. The lower stance is just the tip of the iceberg of the many almost imperceptible details that add up to make this resto-Vette a success.




Street Shop Inc. supplied the complete chassis, including the LT4 crate engine and six-speed transmission. The frame uses C7 Corvette suspension components and geometry and handles like a modern Corvette. The chassis was painted and reassembled before sliding under the body.
“I pay a tremendous amount of attention to detail in my business,” says Kevin. “Tim shares that same passion in building his amazing Corvettes. We worked through every detail together, no matter how small.” When outside work was required, the duo would invite the help of equally-talented craftsmen to move the project forward. Chance Blevins at Blevins Auto did the interior for the car, working with Kevin to find just the right shade of leather. He then fitted it throughout the cockpit, and Kevin states the custom-fitted interior is quite comfy and describes its fitment as superb.

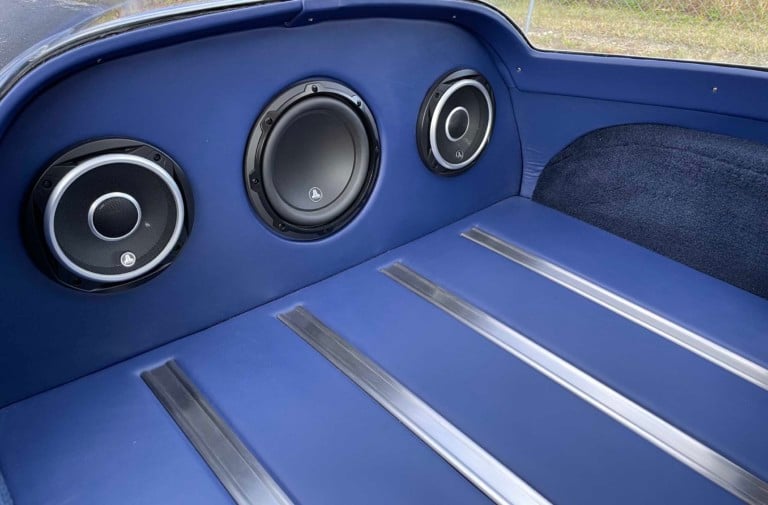
The interior is finished in a stunning blue hue, a testament to the handiwork of Chance Blevins at Blevins Automotive.
Emblems are a great way to make a statement on an all-white exterior, but Kevin didn’t want to shout to get his point across. Keen eyes will note the differences between these emblems from stock, but the changes could easily go unnoticed, a tribute to their subtlety and craftsmanship. Kevin had Andrea Koenig of Motorhead Jewelry in Louisville, Kentucky, make C2-looking emblems with the factory C2-styled “Corvette” combined with a one-word “Stingray” in the C7 font. The side emblems are the original C2 design for a fuel-injected Corvette with the Fuelie tagline swapped out to “Supercharged” in the C7 style. One final design element that could easily go unnoticed includes the custom Classic Instruments gauges combining the C2 Corvette crossed flags and numbers in the C7 Corvette’s font.


The dash panels were treated to custom-designed gauges from Classic Instruments featuring Corvette’s crossed flags. Both the dash and glovebox door were covered to match the interior.
Bridging the gap between generations was mainly the work of Tim and the team at J&M. After the body and chassis was fitted properly, the car was disassembled for the last time so everything could be coated in the appropriate color for the build. The body and frame received their shiny white hue, while the engine compartment received a contrasting color that matched the interior. After the appropriate cutting and buffing, all the components were installed for the last time.

Getting a perfect fit required numerous trial-fit sessions. Once everything was perfect, the body was then removed in preparation for painting. The rear quarter panels were widened to allow those custom-made Brixton Forged wheels with crossed flag center caps to fit between the wheel wells.
Now that the car is finished, Kevin reports that he intends to drive it primarily, but he attests that it looks great, even when sitting at home in his garage.
I would not change or try to improve a single thing on the car. – Kevin Wilkinson
Photo gallery




“The car is a beast, super-fast in all aspects, from acceleration to braking. In addition to the amazing responsiveness, it is super comfortable and tracks beautifully cruising down the highway.”

Coupling those iconic lines with world-class performance is a surefire way to create an amazing driving experience. It only gets better when you include the increased cabin volume to ensure the inhabitants are comfy while doing so. The icing on the cake would be the sound of that unbridled LT4 through the side pipes while it’s all going down!